Operations
Opening Balance
This page refers to the initial quantities and values of stock when you start using the inventory system. It shows the starting figures for each product at the beginning of an accounting period or when the system is first implemented.
Filtering and Sorting:
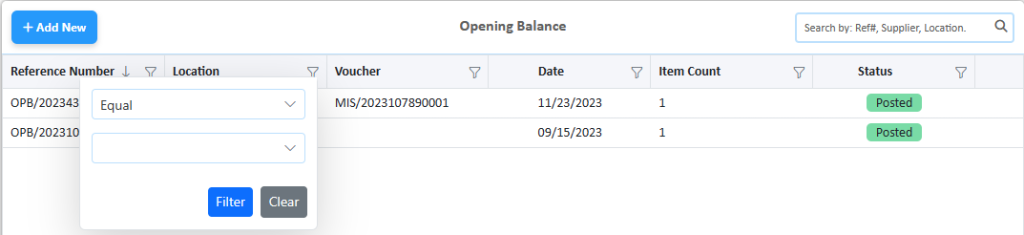
Click on the filter icon to open the filter, and enter the value to filter for or use the search bar to find the desired record.
The records can also be sorted in ascending and descending order of the desired field, simply double-click on the column that should be sorted.
Creating a new opening balance
The user needs to have location access under the current company.
Location:

Select the Location to be targeted.
These are the locations the user has access to under the current company.
Date:

The Date for the opening balance. Once the products are selected the date cannot be changed.
Description:

Enter the desired description.
Products:

Enter the product code OR select from drop down search. then double click on the qty to enter the quantity.
Click on the save button to create this opening balance.
Custom Route Setup
This page allows users to define and customize specific workflows or processes, the custom route with single/multiple stops can be managed.
Add new custom route
Click on the add button to create a new custom route.
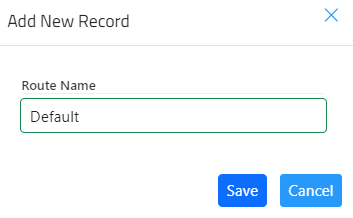
Enter the name of the custom route and click save.
Add more stops:
Select the first stop and second stop, then add the desired description.
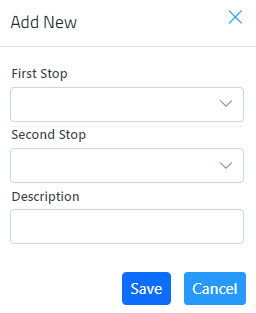
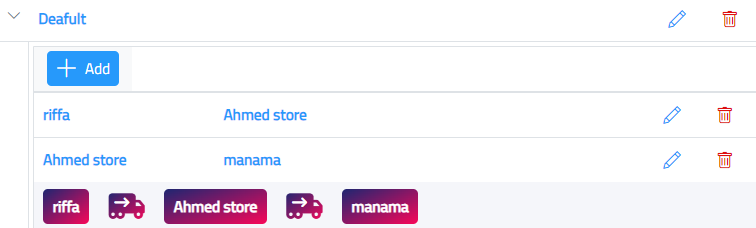
Click save.
To add more stops, follow the previous steps, and the system will automatically set the new first stop as the second stop of the last created entry.
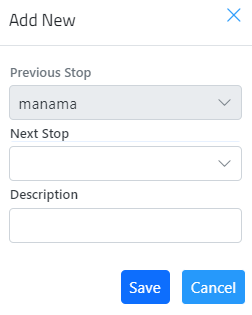
Note: Users can add custom routes only when there are locations in the company.
Delivery Order
This page allows users to manage the process of dispatching products to customers. It includes details about the items to be delivered, Users can create, view, and track delivery orders, ensuring smooth and timely shipment operations.
Filtering and Sorting:
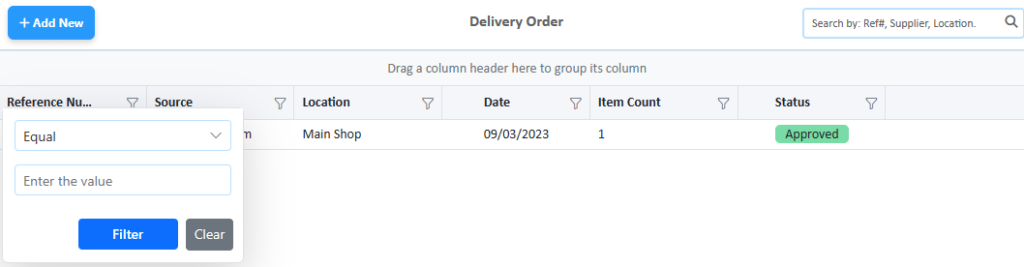
Click on the filter icon to open the filter, and enter the value to filter for or use the search bar to find the desired record.
The records can also be sorted in ascending and descending order of the desired field, simply double-click on the column that should be sorted.
Flow of Document Status
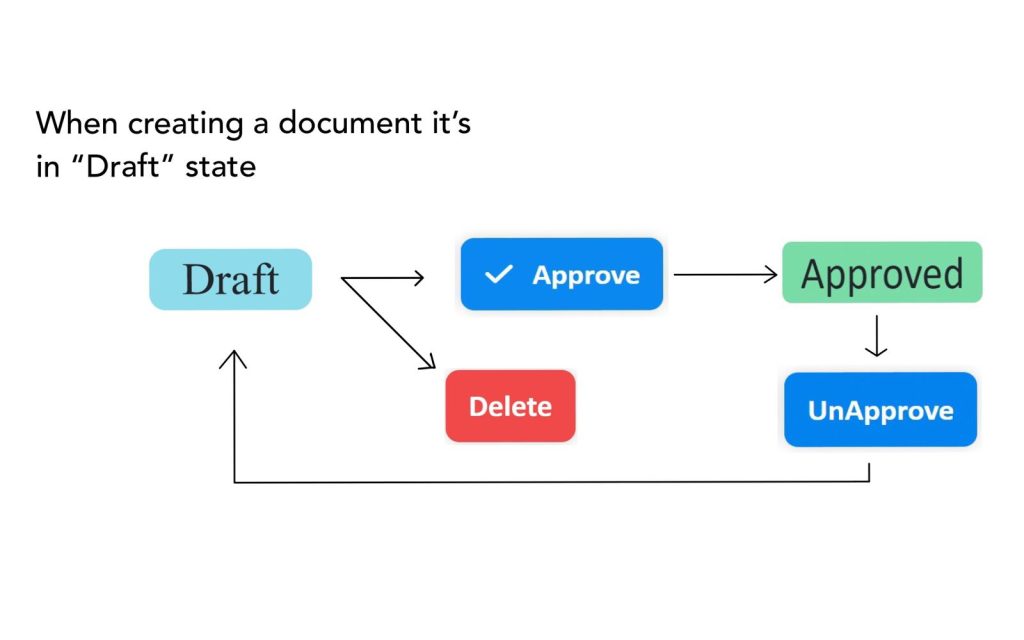
Creating a new delivery order
The user needs to have location access under the current company.
Location:

Select the Location to be targeted (delivered).
These are the locations the user has access to under the current company.
Source:
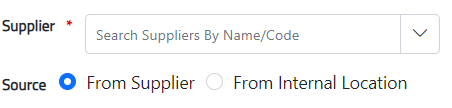
You can select either Supplier which means the products will be delivered directly from an external vendor.
OR Internal location which indicates the goods will be shipped from the company’s own inventory.
Date:

The Date for the delivery order. Once the products are selected the date cannot be changed.
Purchase Representative:
Choose purchase representative from the drop down search.

Description:

Enter the desired remarks.
Products:
Enter the product code directly or select it from a dropdown search for available products, then enter the quantity.

Latest cost will be shown to provide up-to-date pricing information.
Right-Click on a Line for More Actions:

The product Info displays Product Information Like Units, Suppliers, Stock and product history.
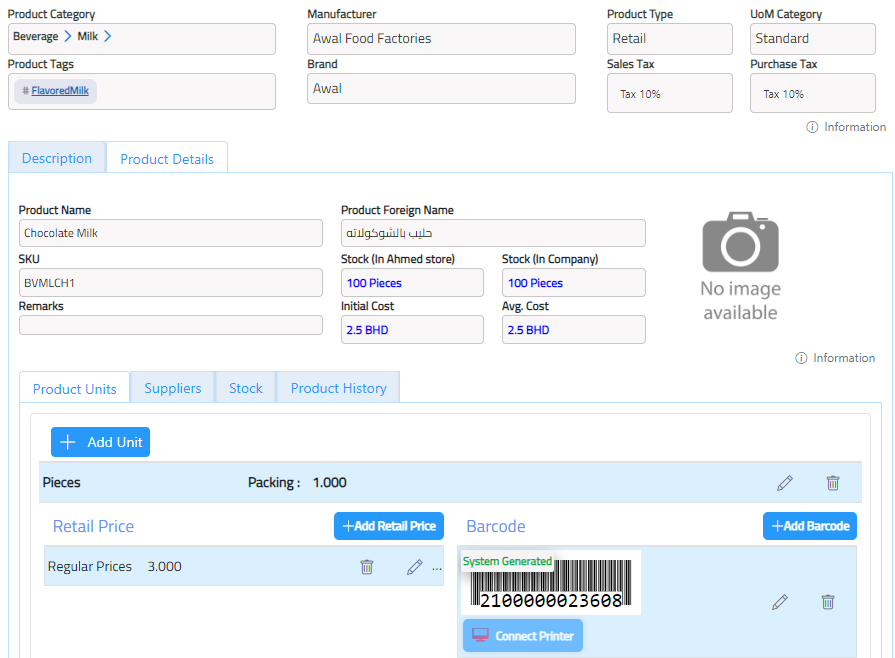
The Product History button displays all transactions for this particular product, including Incoming Quantity, Outgoing Quantity, and Difference Quantity.
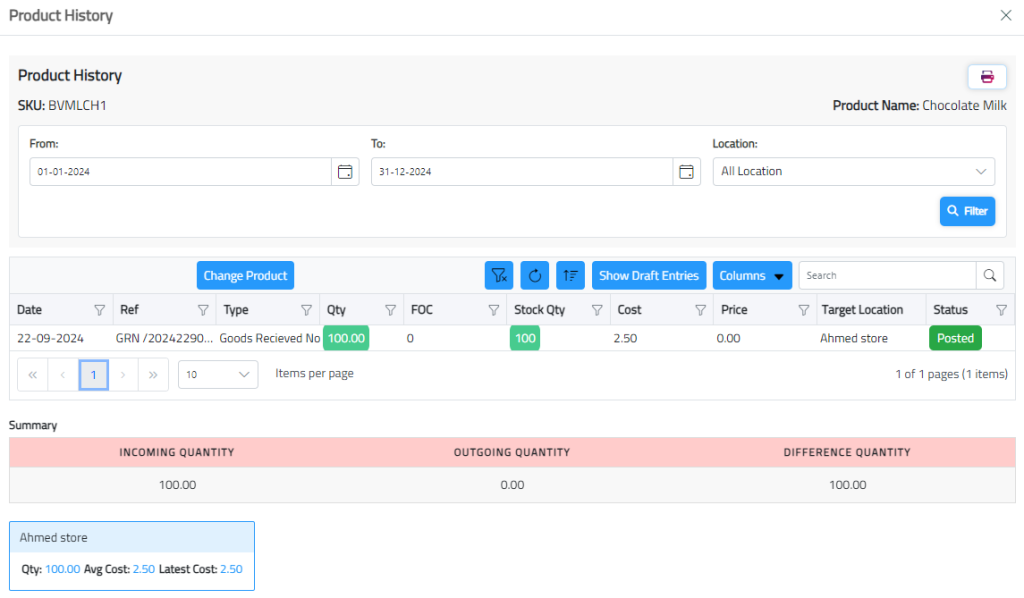

Click on the delete button to delete the document.

Click on the approve button to approve the document.

Click on the print button to export the document in PDF form.
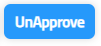
To edit a approve document, user needs to un approve the document and make the necessary changes and approve the document again.
Goods Received Notes
This page is designed for users to manage and record the receipt of goods from suppliers. This page allows users to verify the quantity of items received, ensuring that they match the order specifications. Users can create, view, and track GRNs, facilitating efficient inventory management and ensuring accurate stock levels.
Filtering and Sorting:
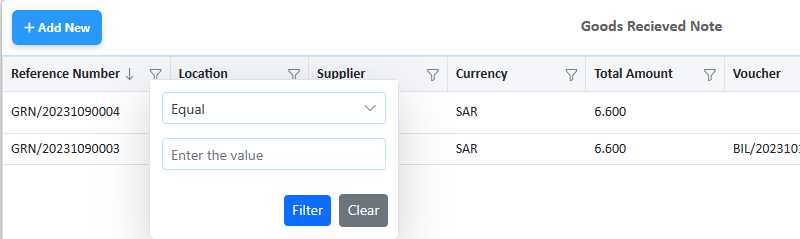
Click on the filter icon to open the filter, and enter the value to filter for or use the search bar to find the desired record.
The records can also be sorted in ascending and descending order of the desired field, simply double-click on the column that should be sorted.
Flow of Document Status
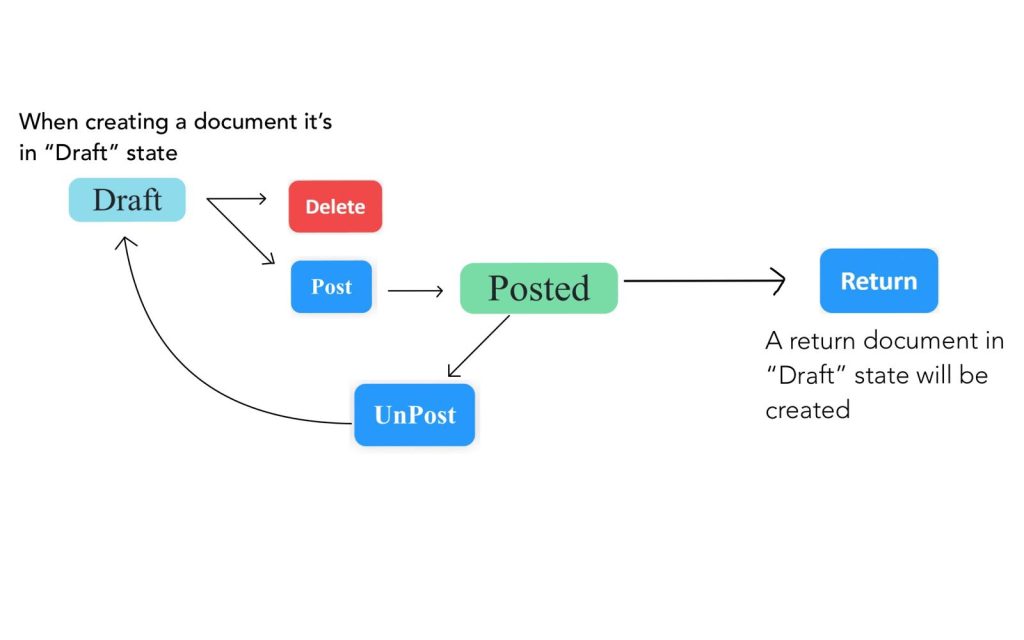
Create a New goods received note
Retrieving from Reference Option:
Search Button: Click the search button to retrieve from purchase order or planned purchase order entered in the module.
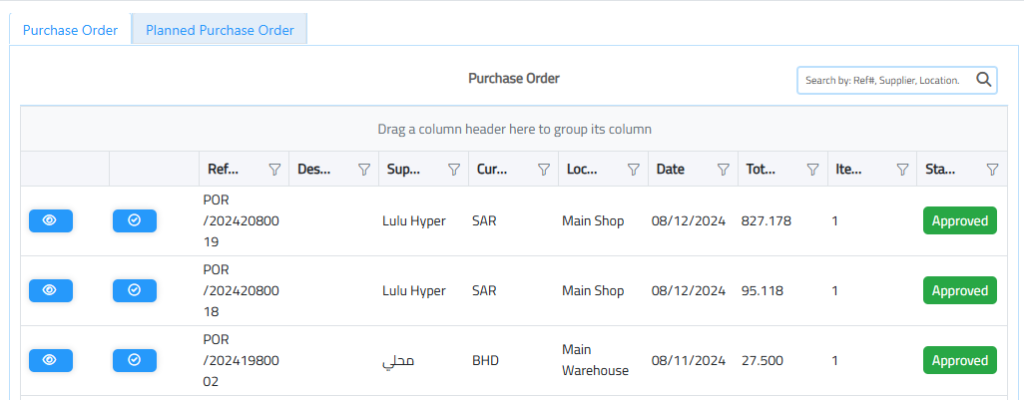
To view a reference before choosing it, click the eye button. | ![]() |
Supplier:

Select the supplier.
Location:

The Location to be targeted.
This cannot be edited once the product is selected.
Date:

Select the Date.
Once the products are selected the date cannot be changed.
Currency:

Select the desired currency.
Tax policy:

Choose the desired taxation policy.
Invoice Number:

in this field you can enter invoice number.
Supplier Products only:

This will show you only products that linked with this supplier
Discount Type:

the discount types are of 2 kinds, discount by each item or by the entire invoice.
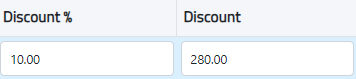
If it’s by type then enter how much discount amount per product in the table. And the system will do the calculations.

But if it is a discount by invoice then enter the discount Percentage.
Purchase representative

The employee who has the responsibility of being a purchase representative.
Price Retrieve Method: Choosing a price retrieval method affects how the price of a product or service is calculated and displayed transactions:
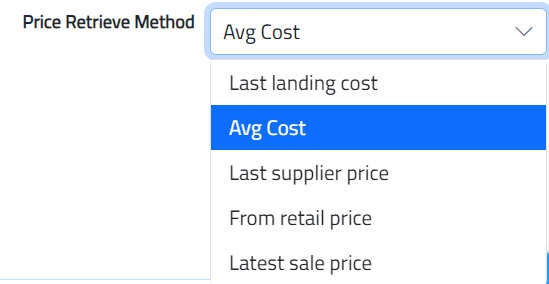
1. Last Landing Cost: This method retrieves the price from the most recent Goods Received Note (GRN), representing the latest cost at which the product was acquired.
2. Average Cost: This method calculates the price based on the average cost of the product over time, considering all previous purchase prices.
3. Last Price from Supplier: This method uses the most recent price provided by the supplier.
4. Retail Price: The retail price is the price specified in the product details at the time of its creation.
5. Last Sale Price: This method displays the price at which the product was last sold to customers, reflecting the most recent sale price.
The default method in GRN is Average cost.
Description:

Enter the desired remarks.
Products:

Enter the product code directly or select it from a dropdown search for available products.

Click on Additional cost tab to add cost to the products, For example : Shipping cost.

Click on Service tab to add service .. For example : warranty
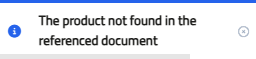
This means that the product you are trying to add does not exist in the list of products associated with the reference you retrieved, ensure that all products you add are already included in the referenced list.
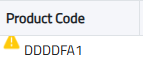
This alert appears when the product is not added to the supplier
Right-Click on a Line for More Actions:

The product Info displays Product Information Like Units, Suppliers, Stock and product history.
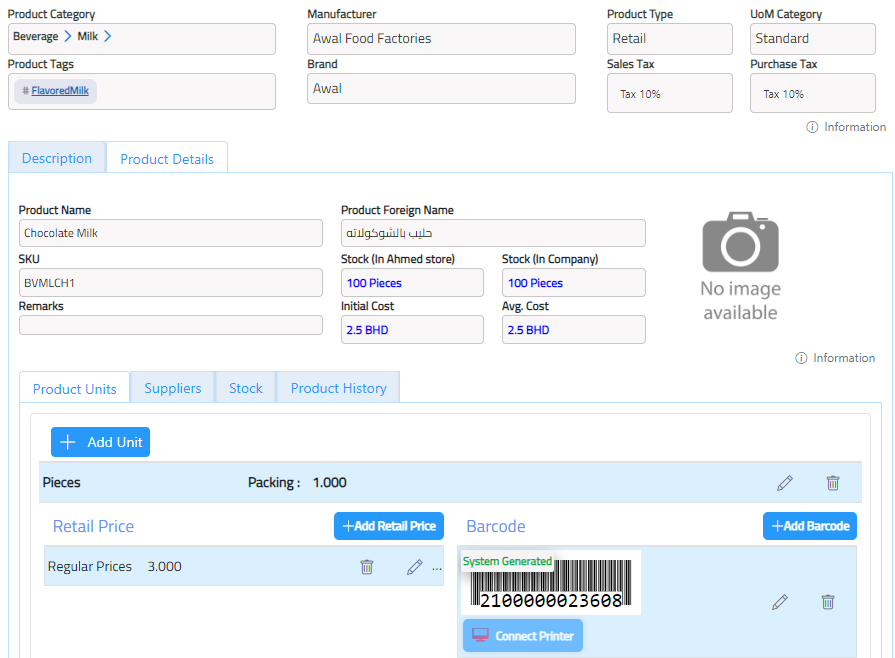
The Product History button displays all transactions for this particular product, including Incoming Quantity, Outgoing Quantity, and Difference Quantity.
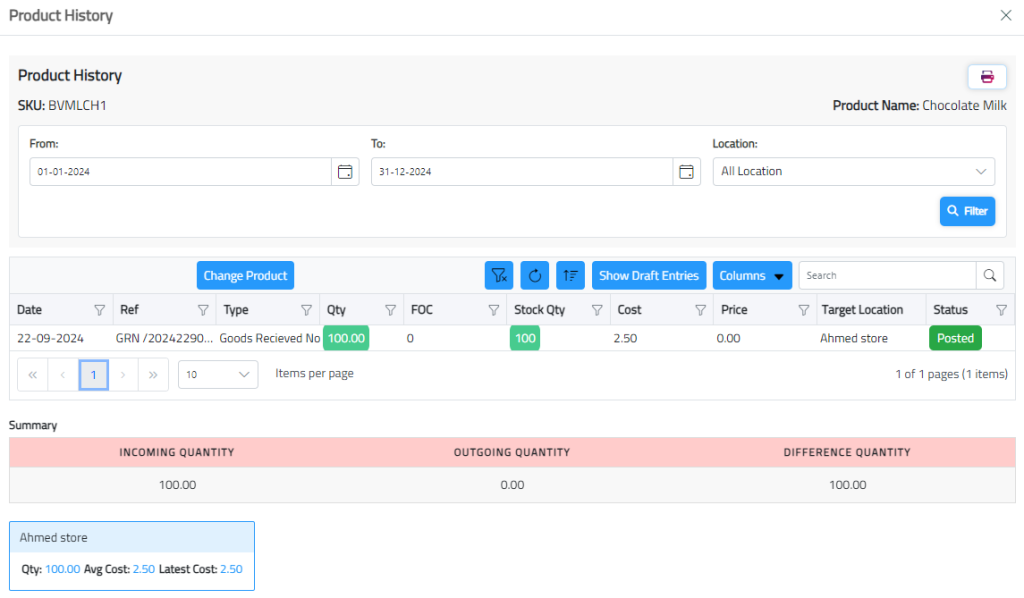
Once the products are selected, you cannot change the information below, Except : Discount, Sales representative and Description.
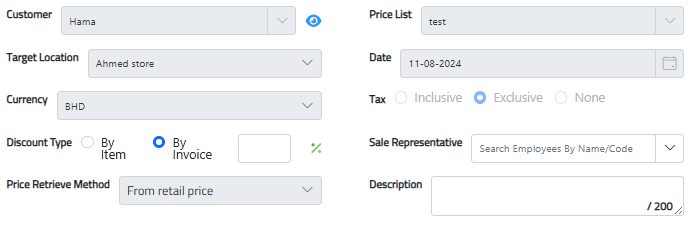

Click on the save button to create this Document.
Once the Record is saved, the Status of the document is Draft.

Click on the delete button to delete the document.
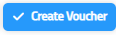
Create a voucher for this record by clicking on the Create voucher button. Voucher reference will show in the bottom.

Click on the print button to export the document in PDF form.

the user can return a GRN by clicking on the button. the system will create a purchase return.
Delivery Note
This page is used for shipments of goods to customers. It provides detailed information about the items being delivered, including descriptions, quantities, and any special instructions. This document serves as a record of the transaction, ensuring that both the sender and recipient are aware of what has been shipped. Users can create, view, and manage delivery notes, facilitating effective communication and record-keeping in the delivery process.
Filtering and Sorting:

Click on the filter icon to open the filter, and enter the value to filter for or use the search bar to find the desired record.
The records can also be sorted in ascending and descending order of the desired field, simply double-click on the column that should be sorted.
Flow of Document Status
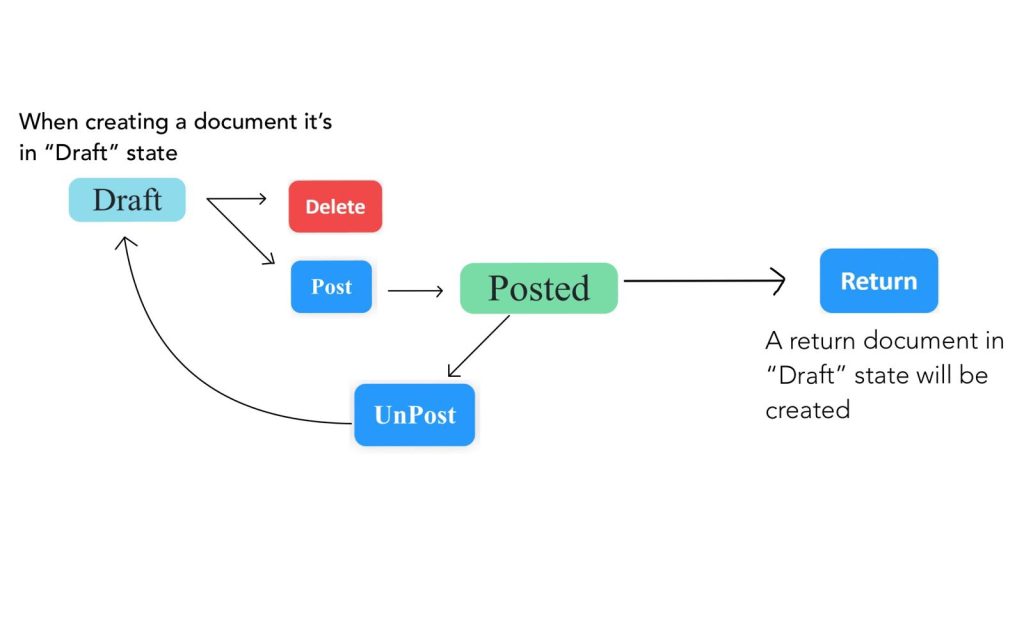
Create new Delivery Note
Retrieving from Reference Option:
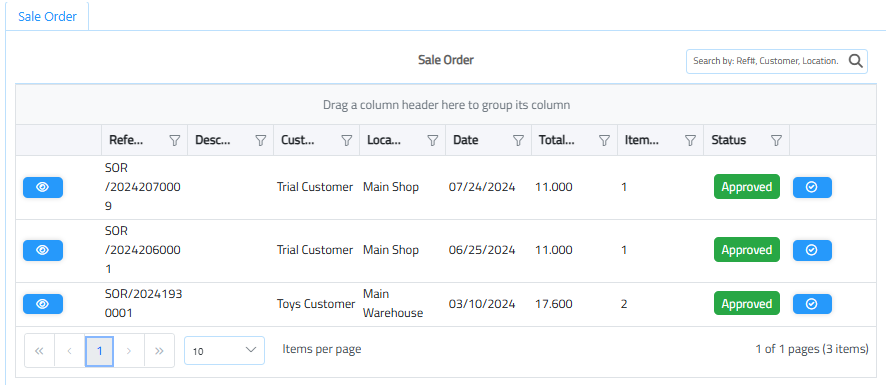
Search Button: Click the search button to retrieve from sale order entered in the module.
To view a reference before choosing it, click the eye button. | ![]() |
Customer :

Select the customer.
Price List:

Once you select a customer, the linked price list will be displayed. However, it cannot be edited.
Location:

The Location to be targeted. This cannot be edited once the product is selected. These are the locations the user has access to under the current company.
Date:

Select the Date. Once the products are selected the date cannot be changed.
Currency:

Select the desired currency.
Tax policy:

Choose the desired taxation policy.
Discount Type:

the discount types are of 2 kinds, discount by each item or by the entire invoice.
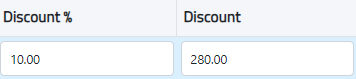
If it’s by type then enter how much discount amount per product in the table. And the system will do the calculations.

But if it is a discount by invoice then enter the discount Percentage.
Sale representative:

The employee who has the responsibility of being a sales representative.
Price Retrieve Method: Choosing a price retrieval method affects how the price of a product or service is calculated and displayed transactions:
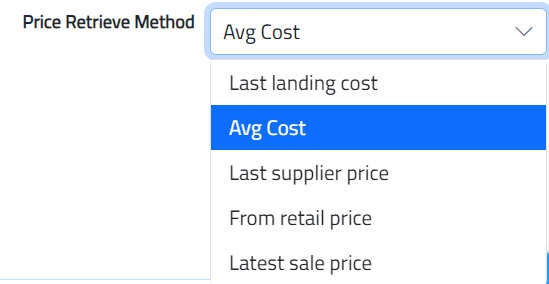
1. Last Landing Cost: This method retrieves the price from the most recent Goods Received Note (GRN), representing the latest cost at which the product was acquired.
2. Average Cost: This method calculates the price based on the average cost of the product over time, considering all previous purchase prices.
3. Last Price from Supplier: This method uses the most recent price provided by the supplier.
4. Retail Price: The retail price is the price specified in the product details at the time of its creation.
5. Last Sale Price: This method displays the price at which the product was last sold to customers, reflecting the most recent sale price.
The default method in delivery note is retail price.
Description:

Enter the desired remarks.
Products:

Enter the product code directly or select it from a dropdown search for available products.
Latest cost will be shown to provide up-to-date pricing information.
Book Quantity: Refers to the stock quantity in the chosen unit.
Average Cost: Represents the cost in the chosen unit.
Amount: The total amount before applying taxes and discounts.
Right-Click on a Line for More Actions:

The product Info displays Product Information Like Units, Suppliers, Stock and product history.
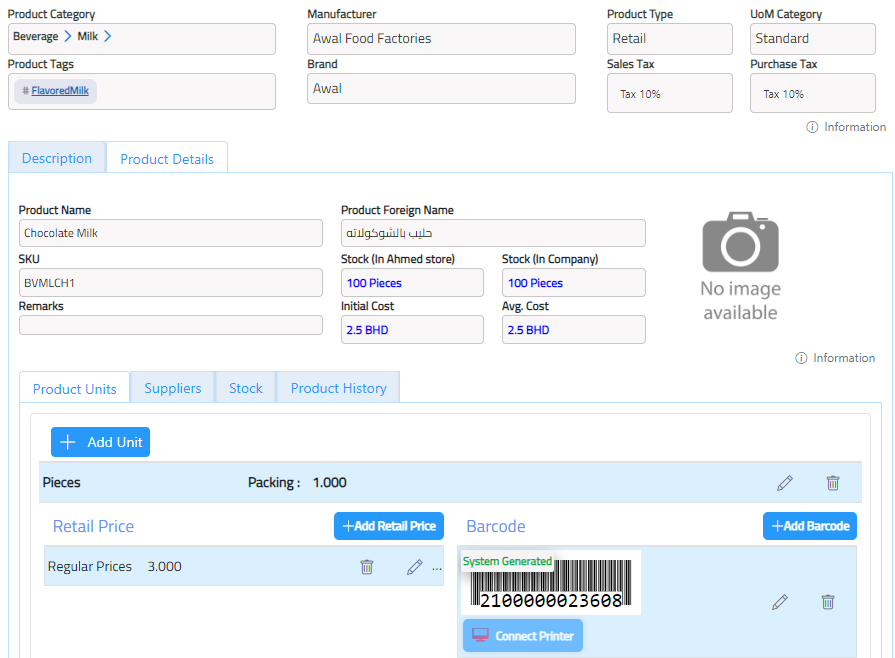
The Product History button displays all transactions for this particular product, including Incoming Quantity, Outgoing Quantity, and Difference Quantity.
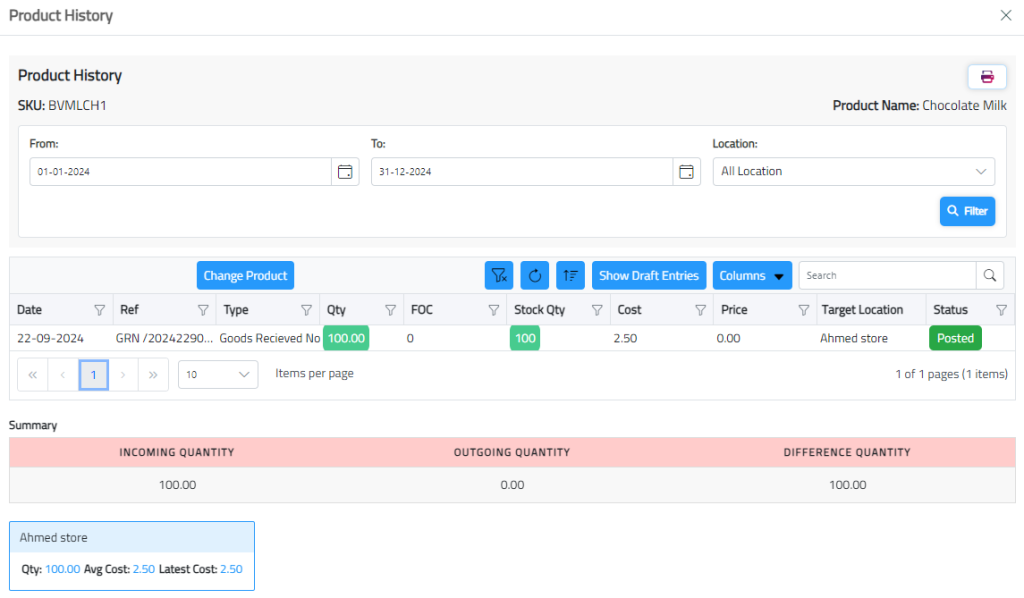
Expiry Date:

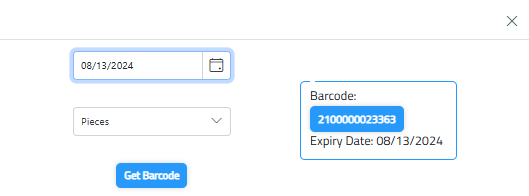
If you select a product with an expiration date, a message will appear, you have to click “Get Barcode” to continue using the product.
Click on the save button to create this Document. Once the Record is saved, the Status of the document is Draft.
Click on the delete button to delete the document.
Once approved the user can easily create a voucher by clicking on the button. and the system will will display a reference number in the bottom.
the user can return a delivery note by clicking on the button. the system will create a credit note.
Click on the print button to export the document in PDF form.
If the user has permission, click the unpost button to unpost the document.
Click the duplicate button to create a copy of the document.
Transfers
Transfer Send
The Internal transfer page allows users to initiate the internal transfer of stock between different locations within the company. Users can select the source location, specify the destination location, and list the items being transferred along with their quantities.
Filtering and Sorting:

Click on the filter icon to open the filter, and enter the value to filter for or use the search bar to find the desired record.
The records can also be sorted in ascending and descending order of the desired field, double-click on the column that should be sorted.
Note: The internal transfer document should be sent, only then can it be retrieved in the transfer receive
Document Status:
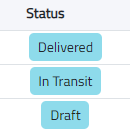
Delivered: Items have been successfully transferred and received at the destination.
In Transit: Items are on the way from the source to the destination; stock is deducted from the source but not yet received.
Draft: The transfer is still in progress and not finalized, no stock movement has occurred.
Flow of Document Status
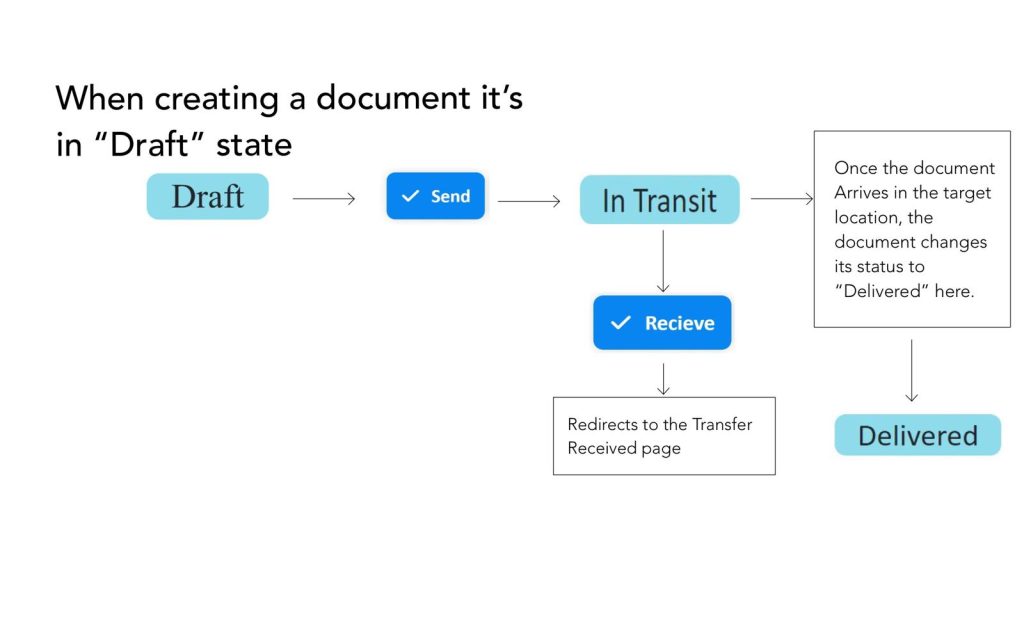
Create new Internal Transfer
Location:

Select the source location from which goods will be transferred. And Choose the destination location where goods will be received.
Date:

The Date for the internal transfer. Once the products are selected the date cannot be changed.
Remarks:
Enter the desired remarks.
Products:
Enter the product code directly or select it from a dropdown search for available products.

To be able to send the document the company should have a default account for inventory transfers chosen in the company’s chart of accounts on the company setup page on the setup tab in the accounting module.

The user can print this document by clicking on the print button and the system will convert the document to a PDF to be printed or downloaded and saved.

The “Send” button initiates the transfer of goods from the source location and updates the inventory records to reflect the outgoing items
When you receive the transfer, you have to Click on “receive” button. you will be redirected to the receiving page, where you can confirm receipt at the destination location, completing the transfer and updating the inventory accordingly.

Transfer Receive
This page is used to document the receipt of stock transferred from another location within the organization. Users can confirm the items received, update quantities, and resolve any discrepancies between the expected and actual items.
Filtering and Sorting:

Click on the filter icon to open the filter, and enter the value to filter for or use the search bar to find the desired record.
The records can also be sorted in ascending and descending order of the desired field, double-click on the column that should be sorted.
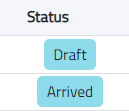
Draft: The transfer is still in progress and not finalized, no stock movement has occurred.
Arrived: Items have reached the destination.
Create a new transfer receive
Click on add new, then click on the search button


Select from internal transfers documents.

Click on the button to view document first | ![]() |
Click on the button to select the document | ![]() |
If you select additional products, this message will appear:
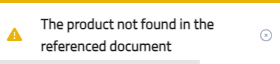
Return transfer:

The document can be returned by clicking on the return button.
Internal Return
This page facilitates the process of returning items to suppliers or vendors. Users can select the products being returned, specify quantities, and provide reasons for the return. This page helps manage returns efficiently, ensuring that the inventory is adjusted accordingly and that any necessary supplier communications are initiated.
Filtering and Sorting:

Click on the filter icon to open the filter, and enter the value to filter for or use the search bar to find the desired record.
The records can also be sorted in ascending and descending order of the desired field, double-click on the column that should be sorted.
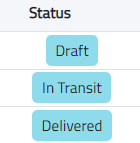
Draft: The transfer is still in progress and not finalized, no stock movement has occurred.
In transit: Transfer sent but not yet delivered.
Delivered: Transfer successfully delivered.
Flow of Document Status
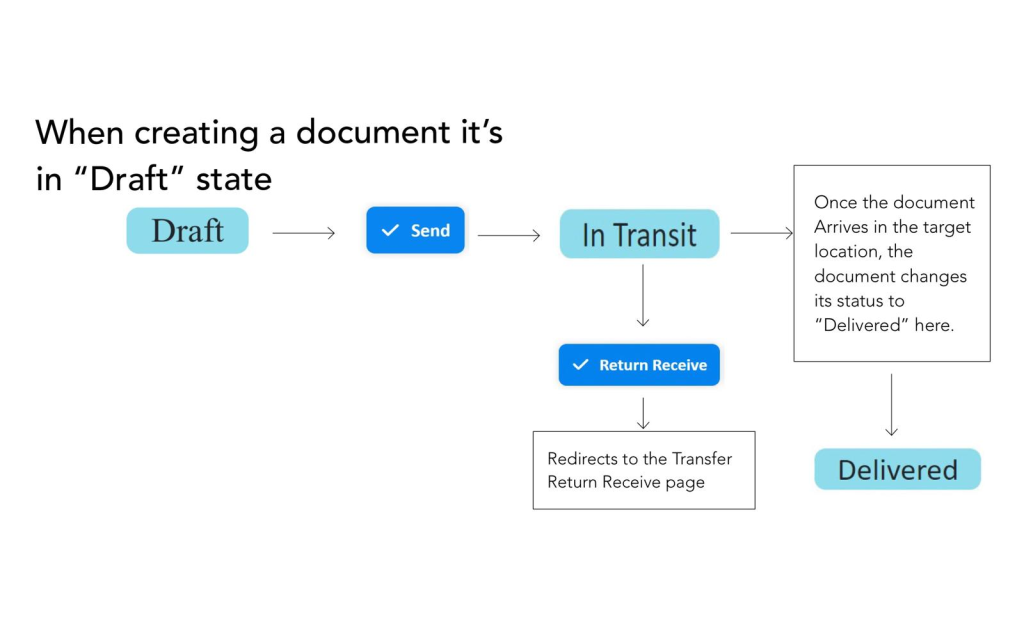
The internal transfer return document should be sent, only then can it be retrieved in the transfer returned received, to be able to send the document the company should have a default account for inventory transfers chosen in the company’s chart of accounts on the company setup page on the setup tab in the accounting module.
Create new internal return
Click on add new, then click on the search button


Select from internal transfers receive documents.

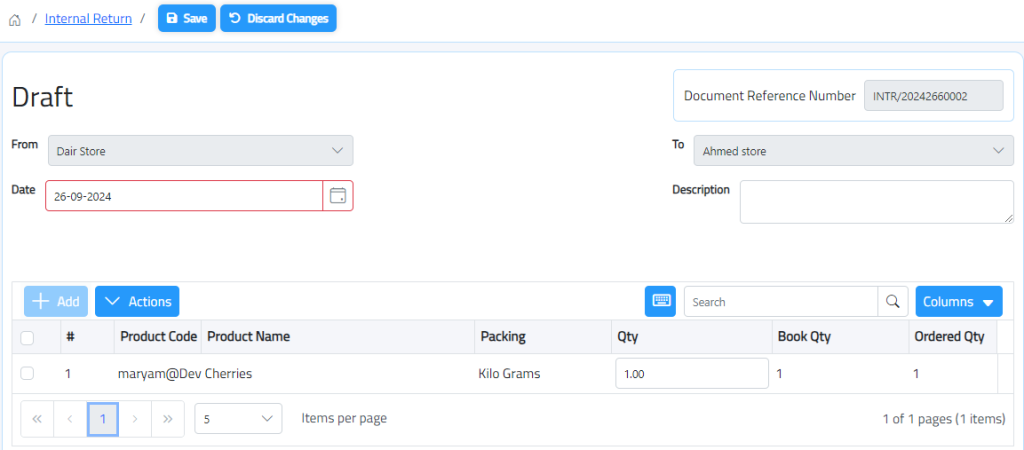
Click on save button to send the document, the document will be in Draft Status | ![]() |
Click on Send button to send the document, the document will be in Transit Status | ![]() |
Click on Return Receive to receive the document, the document will be in Delivered Status | ![]() |
After that you will be redirected to Internal Return (Receive) page.
Internal Return Receive
This page is used to confirm the receipt of returned items. Users can document the products returned and update inventory levels.
Filtering and Sorting:

Click on the filter icon to open the filter, and enter the value to filter for or use the search bar to find the desired record.
The records can also be sorted in ascending and descending order of the desired field, double-click on the column that should be sorted.
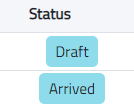
Draft: The transfer is still in progress and not finalized, no stock movement has occurred.
Arrived: Transfer successfully arrived to final location.
Flow of Document Status
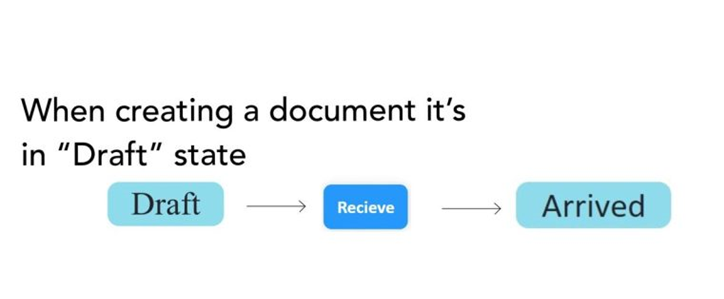
Create new Internal Return Receive
Click on add new, then click on the search button


Select from internal return documents.
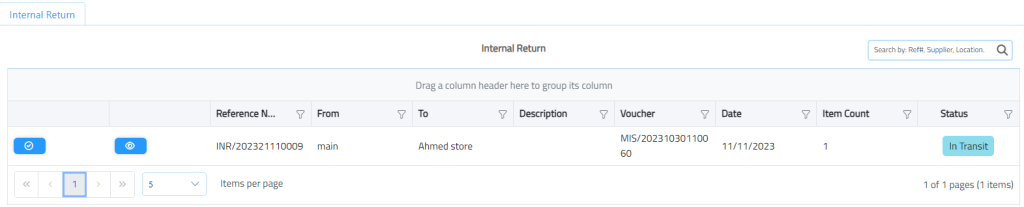
Click on save button to receive the document, the document will be in Draft Status | ![]() |
Click on receive button to receive the document, the document will be in Arrived Status | ![]() |
Adjustment
Inventory adjustment helps to correct stock levels when there missing items or damaged goods. It ensures that the numbers in the system match the actual items available. It helps businesses avoid running out of stock or having too much, and keeps everything accurate for financial records.
Filtering and Sorting:

Click on the filter icon to open the filter, and enter the value to filter for or use the search bar to find the desired record.
The records can also be sorted in ascending and descending order of the desired field, double-click on the column that should be sorted.
Flow of Document Status
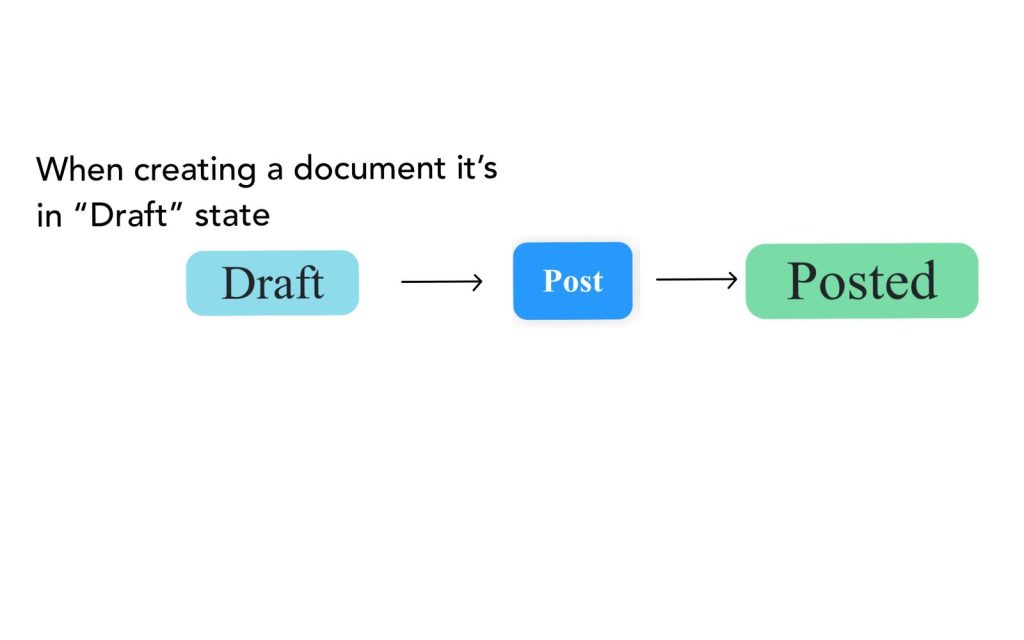
Create a New Adjustment
First, Choose the reason for adjustment:
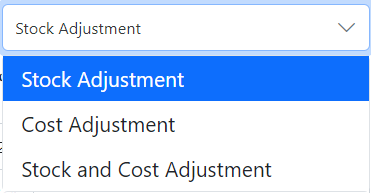
- Stock Adjustment: Record the actual quantity of items.
- Cost Adjustment: Update the cost of items while keeping the stock quantity unchanged.
- Cost and Stock Adjustment: Modify both the cost and the stock quantity.
Note: Add new reasons in setup page > Adjustment reason setup.
Select the target location.

Select the date.

Write a description.

If Stock adjustment reason is selected:


the quantity field will be open for modification, while the cost field remains closed.
If Cost adjustment reason is selected:


f you choose the reason “Cost Adjustment”, only the cost field will be editable, while other fields like quantity will be locked
Note: Fields depends on the reason setup you have configured in the setup page.
Click on Post button to post the document | ![]() |
Once the voucher is posted. you can create a voucher by clicking on Create Voucher button. The voucher can be viewed by clicking on the link or by going to the accounting module.
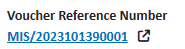
The user can print this document by clicking on the print button | ![]() |
Supply Order
The page is for managing the purchasing of goods. It facilitates the ordering process by allowing users to track and manage supplies needed for inventory replenishment, ensuring efficient procurement and accurate inventory levels.
Filtering and Sorting:

Click on the filter icon to open the filter, and enter the value to filter for or use the search bar to find the desired record.
The records can also be sorted in ascending and descending order of the desired field, simply double-click on the column that should be sorted.
Flow of Document Status
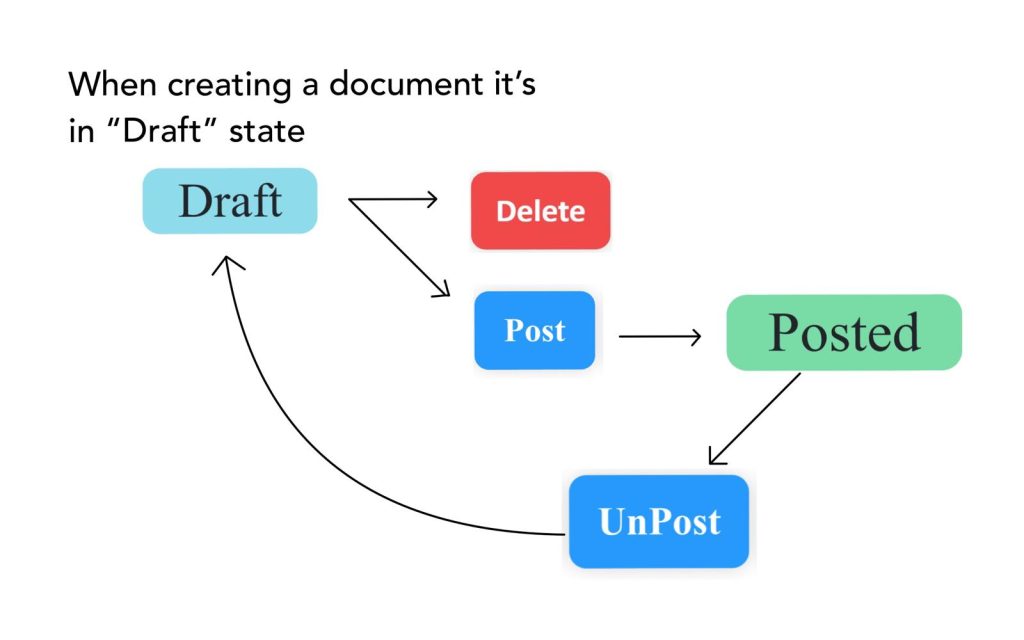
Create a new Supply Order
Here are the steps to create a supply order in an inventory system:

Select the Partner: identifying whether the order is from a supplier or a customer.

Choose Representative: Select the representative responsible for handling the order. This ensures that the correct personnel is assigned to the transaction.

Specify Target Location: Indicate the target location where the goods will be delivered.
Choose the Product: From the available inventory, select the products that are needed for the order.

Enter Quantity: Input the quantity of each product required for the order. and the system will display the book quantity, providing a clear view of the stock being ordered and helping to manage inventory levels accurately.
Right-Click on a Line for More Actions:

The product Info displays Product Information Like Units, Suppliers, Stock and product history.
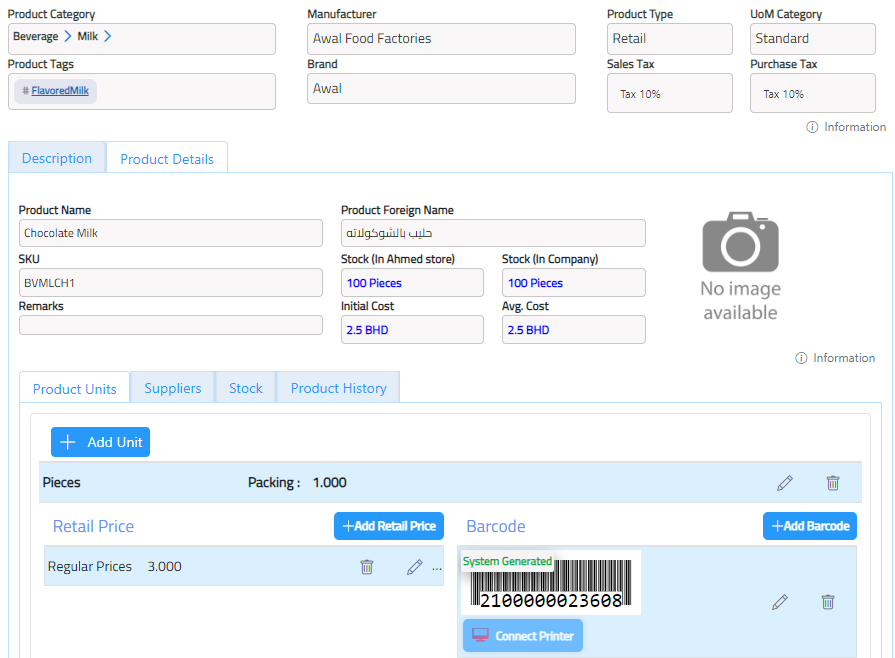
The Product History button displays all transactions for this particular product, including Incoming Quantity, Outgoing Quantity, and Difference Quantity.
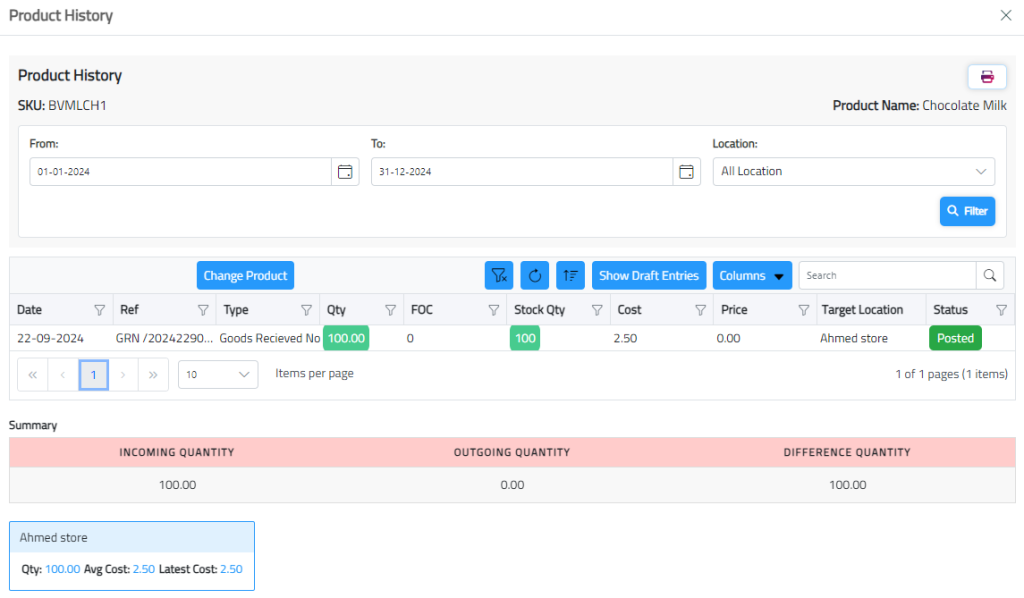
Click on the save button to create this supply order.

Supply order can be duplicated, posted, or deleted.
The user can print this document by clicking on the print button and the system will convert the document to a PDF to be printed or downloaded and saved.
Release Order
This page is designed to manage the dispatch of goods that have been prepared for delivery. This page allows users to confirm and authorize the release of products from inventory to customers or other locations.
Filtering and Sorting:
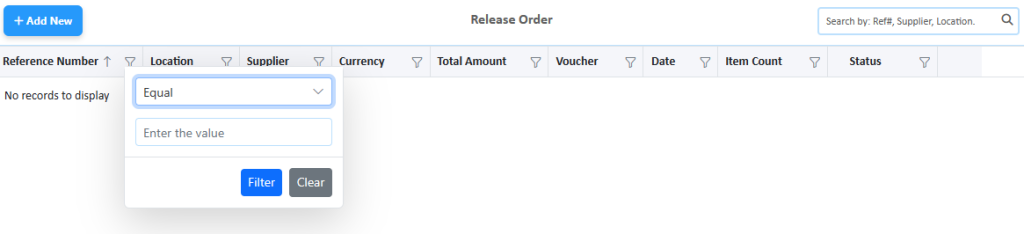
Click on the filter icon to open the filter and enter the value to filter for or use the search bar to find the desired record.
The records can also be sorted in ascending and descending order of the desired field, double-click on the column that should be sorted.
Flow of Document Status
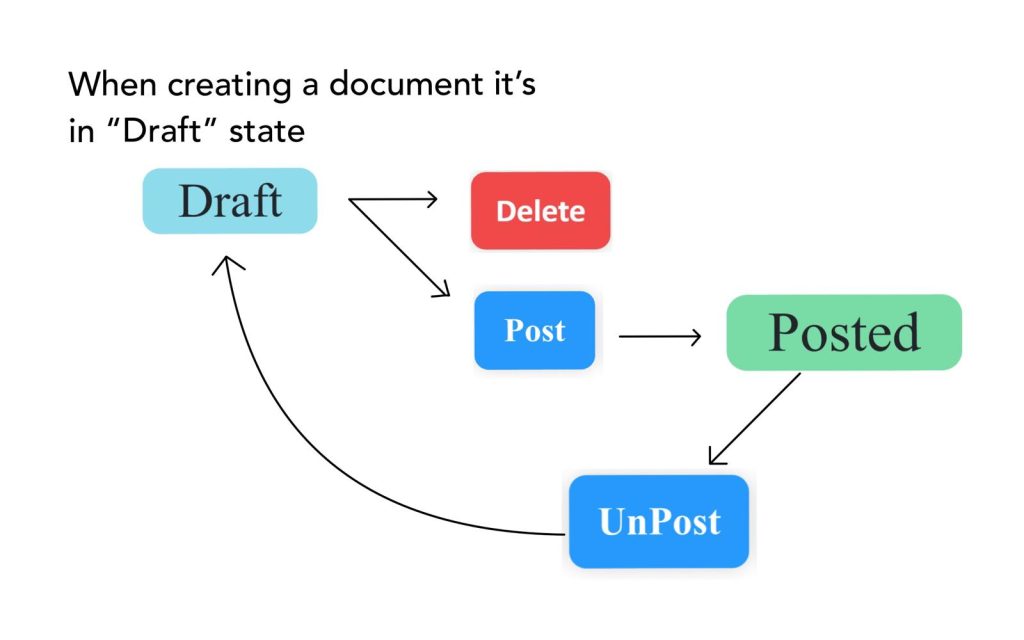
Create a new Release Order

Choose Partner: Selecting the partner type, which can be a customer, supplier, or account, to whom the goods will be released.

Select Representative: Choose the representative responsible for handling the release order.

Select Target Location: Indicate the target location where the goods will be dispatched.

Date: the Date for the release order. Once the products are selected the date cannot be changed.

Select Product: From the available inventory, select the specific products that are to be released and Input the quantity of each product being released in the order.
Right-Click on a Line for More Actions:

The product Info displays Product Information Like Units, Suppliers, Stock and product history.
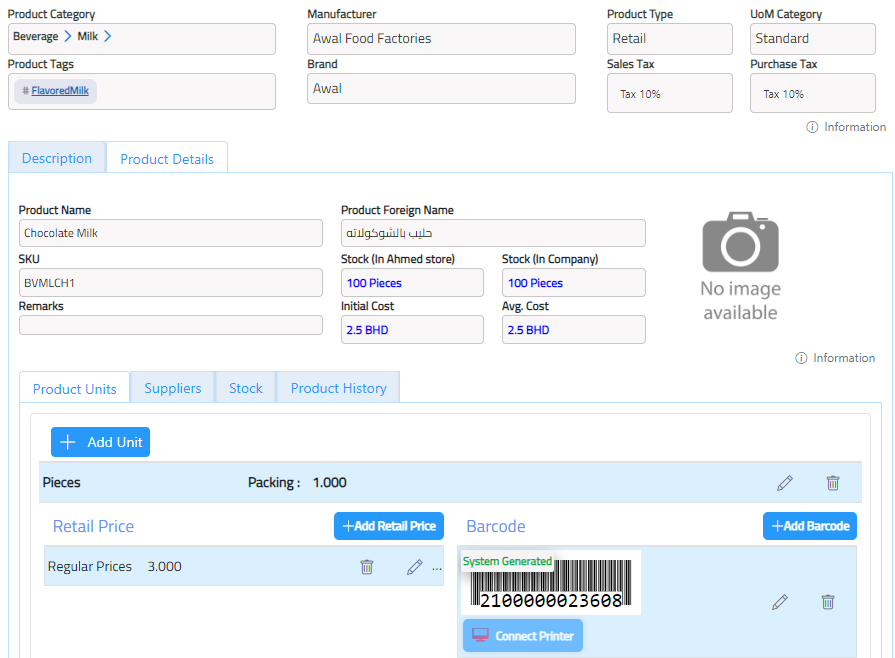
The Product History button displays all transactions for this particular product, including Incoming Quantity, Outgoing Quantity, and Difference Quantity.
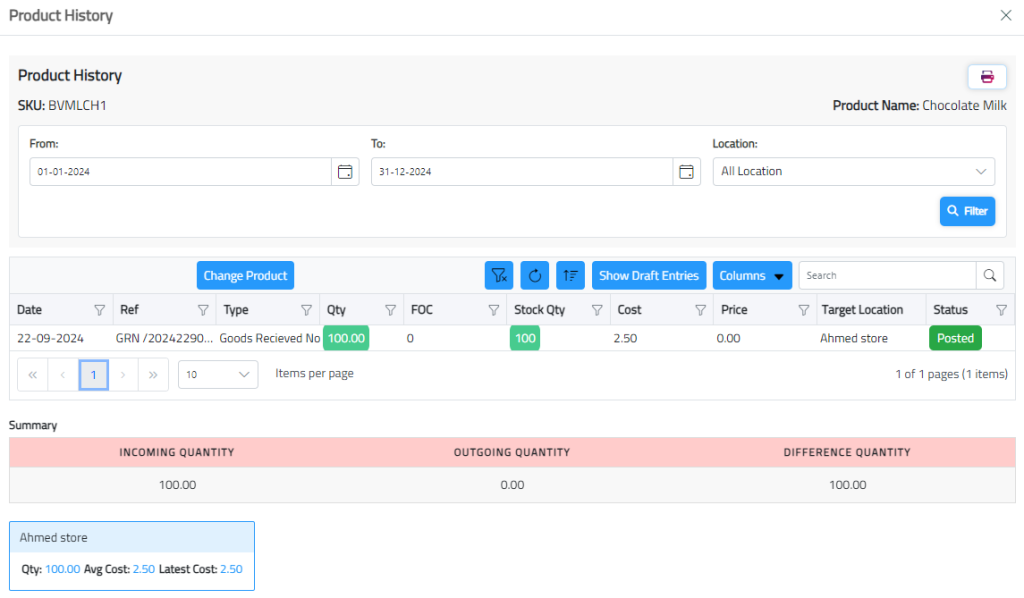
Click on the save button to create this release order.

Release order can be duplicated, posted, or deleted.
The user can print this document by clicking on the print button and the system will convert the document to a PDF to be printed or downloaded and saved.